Briefly about PVD coatings...
PVD is an English acronym for "Physical Vapor Deposition" and is a method for creating hard coatings from ionizing metal vapor. The process takes place in a vacuum chamber, where in the first phase the chamber and tools are heated to a certain temperature, depending on the type of coating, tool, and application. The process can also occur at room temperature, but with a higher temperature (from 200 °C to more than 500 °C) we provide the substrate on which the coating is applied with, a higher level of energy, resulting in better adhesion and coating structure.
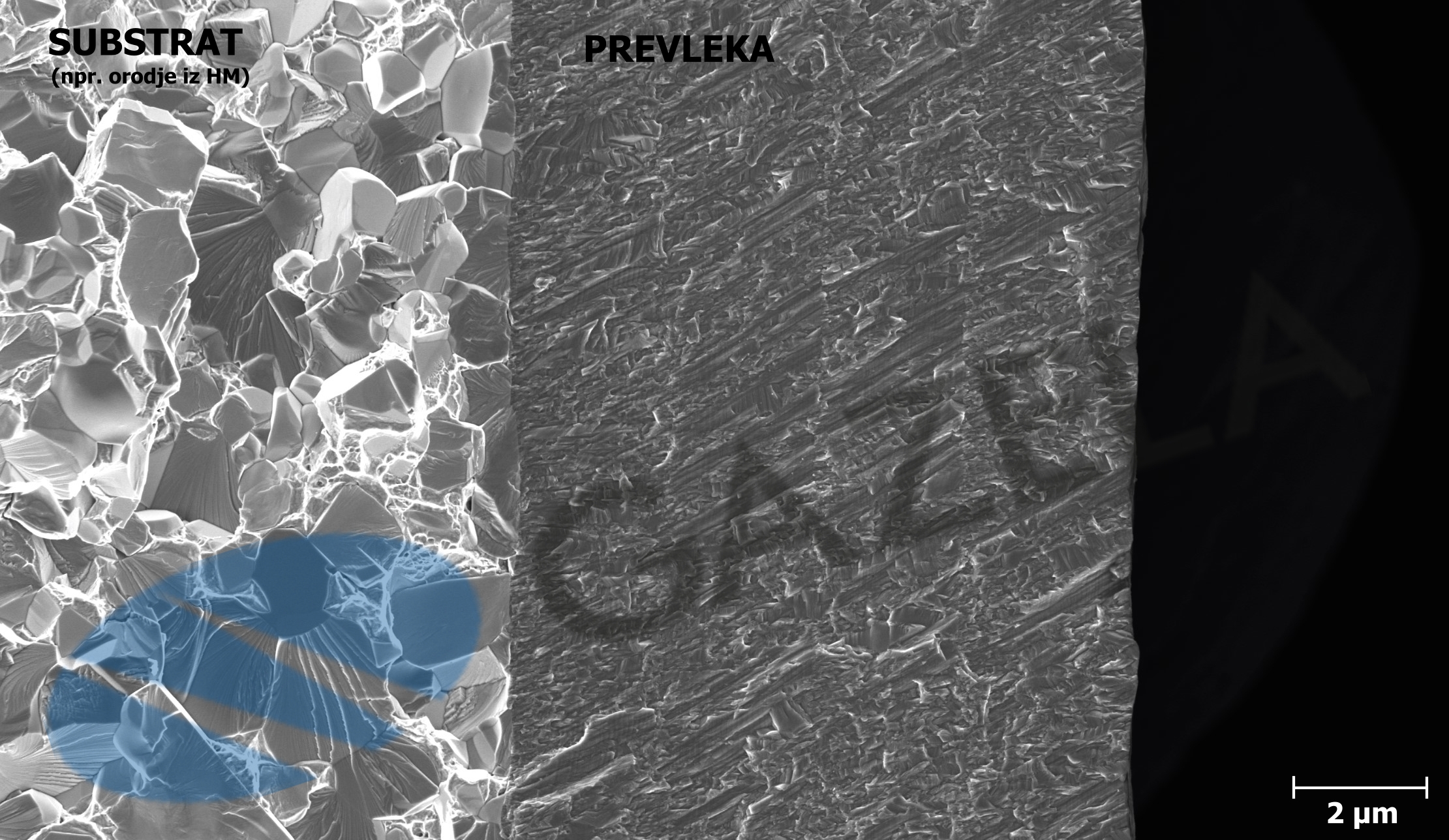
The most common technologies for applying PVD hard coatings are cathodic arc evaporation and magnetron sputtering. PVD deposition methods are atomic in nature and the coating is formed from individual atoms or smaller clusters. The main parameters that affect the structure and quality of coating application are cathode material, working and reactive gases, kinetic energy of particles, temperature and cleanliness of the substrate surface.
The magnetron sputtering process takes place at a lower pressure than the ARC process, and as a result, the coating roughness achieved with this process is lower. When sputtering, we need a large proportion of working - inert - gas (argon or krypton). Molecules of this gas collide at high speed with the target of the material on the cathode that we want to vaporize, and create ions of this material (eg Ti+). These ions bind in the chamber with a reactive gas (eg N2 or C2 or O2 etc.) and form a ceramic layer of a hard coating (eg TiN) on the surface of the tool.
Another method of application is the ARC process, where, unlike the described sputtering method, the erosion of the cathode is achieved by melting and vaporizing solid and molten particles, which happens on very small areas on the cathode of only a few micrometers in size, where a current of extremely high energy density flows in a very short time time. With high-quality cooling of the cathode through its core, material from the cathode can continuously pass into vapor at points without the entire cathode melting. The cathode paths move quickly and randomly over the surface of the cathode, so that we get homogeneous wear of the cathode through almost the entire surface and, consequently, a homogeneous thickness and structure of the resulting coating layer on the tool.
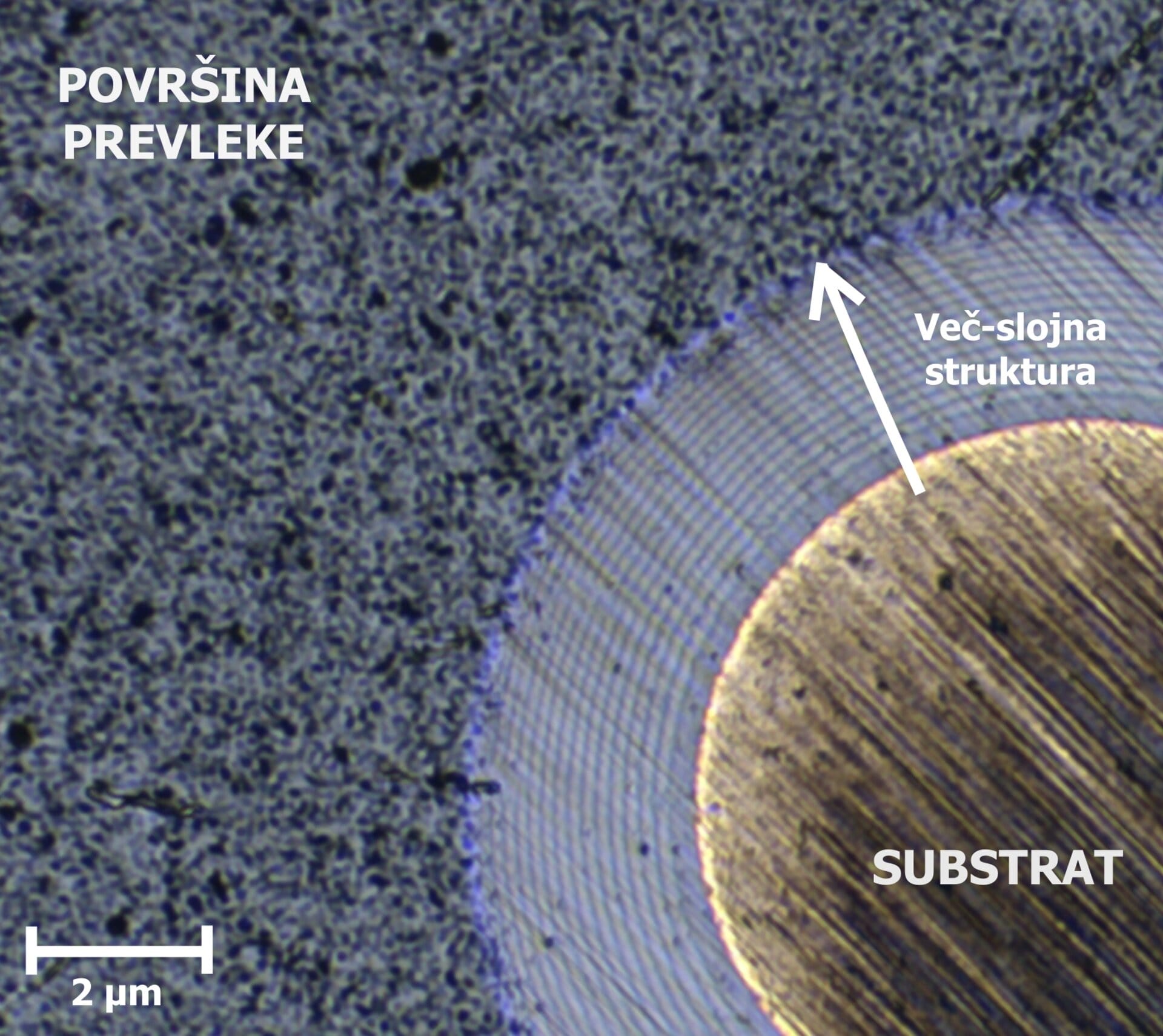
How we ensure quality at Gazela...
In addition to standard measurements of coating thickness and adhesion, the laboratory is also equipped with an instrument for measuring the hardness of thin layers - a nanoindenter, where in the case of coatings only ~ 100 nm is penetrated to a depth. We have as well an instrument for analytical measurement of adhesion - a scratch tester, an instrument for tribological measurements of the coefficient of friction and wear, a confocal microscope for surface analysis and more.
Instruments in the laboratory:
• Thickness measuring instrument
• Rockwell indenter to determine adhesion according to the HF standard
• Scratch test for adhesion
• Nanohardness meter
• Meter of coefficient of friction and coating wear
• Confocal microscope
• Salt bath for corrosivity test (NSS test)
• Contourograph
• Color spectrometer
• Other microscopes and instruments
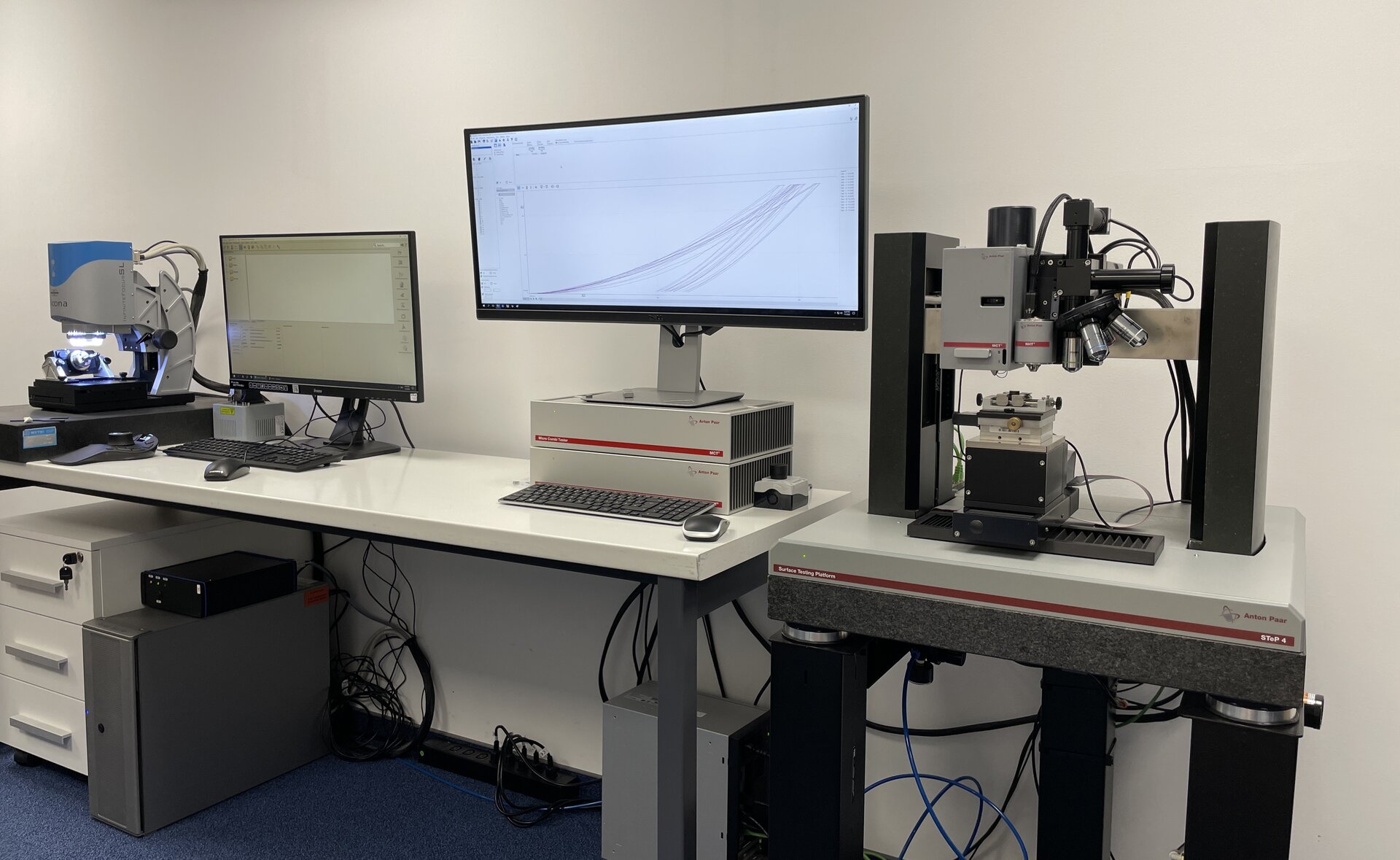
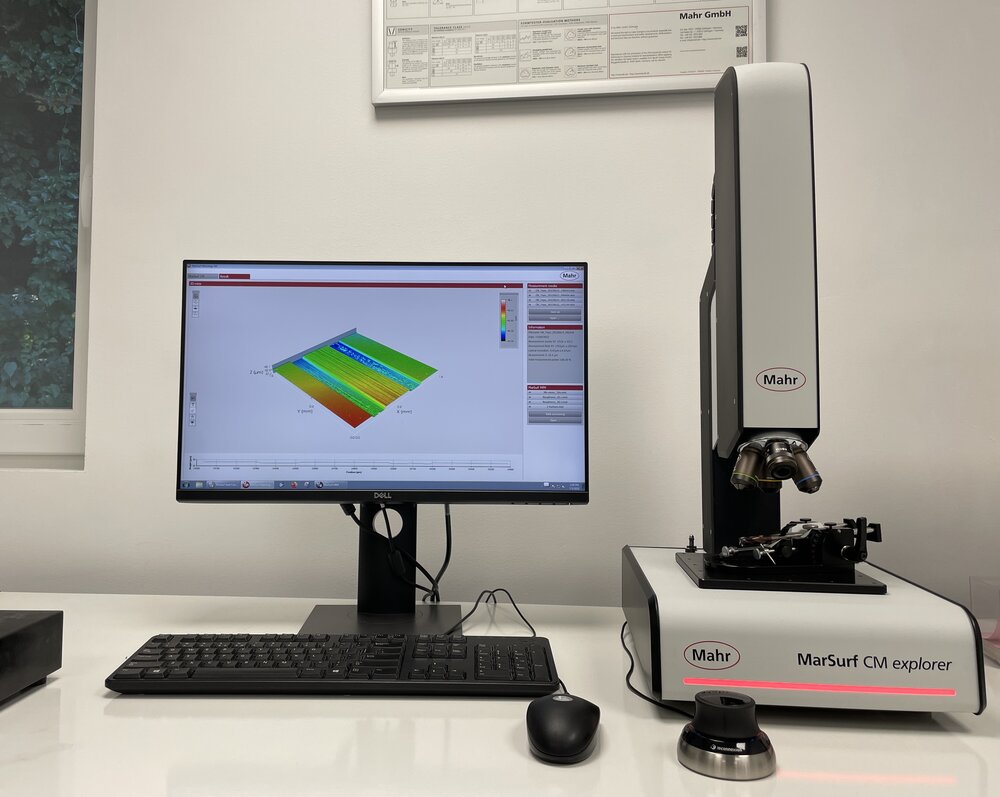
CLICK TO CHOOSE PVD COATING
Removing existing coating
The stripping process is required to remove worn coatings before we apply our PVD coating to your tools or components. Removing the old coating enables better adhesion of the new PVD layer. Either chemical stripping or, in rare cases, mechanical stripping can be used.
We can remove the following layers from your tool:
TiN/TiCN |
HSS, HM |
TiAlN/TiAlCN/TiAlSiN, AlCrN |
HSS, HM |
DLC |
HSS, HM |
CrN |
HSS |
If you are unsure or have any questions, please contact us.